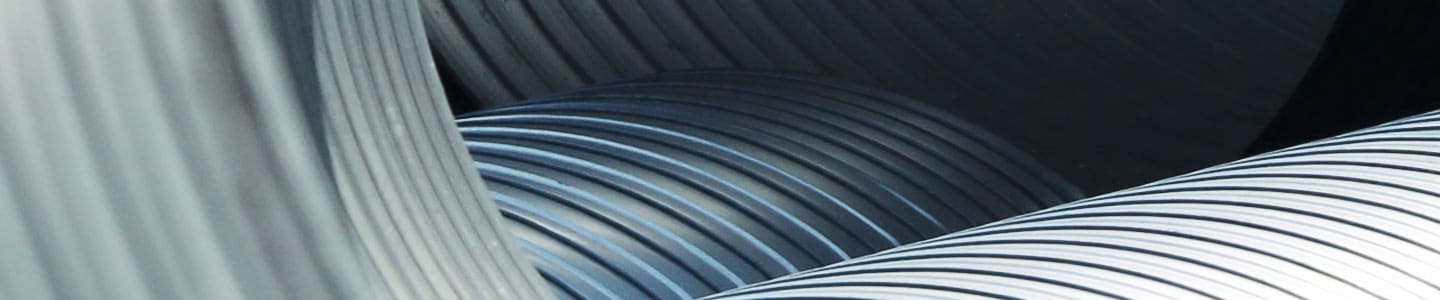
Machine Safeguarding 101: Optimize for Productivity & Safety
June 19, 2024
Machine Safeguarding 101: Optimize for Productivity & Safety
As a business owner, it’s important to ensure that your operations are optimized for improved productivity and worker safety. One of the key components in achieving this goal is machine safeguarding.
Machine safeguarding empowers you to improve worker safety with devices such as guards, shields, sensors, and emergency stops. Far from an interference, these tools enhance the productivity of your operations when implemented by professionals.
In this article, the machine safeguarding experts at Stronghold Safety Engineering discuss the various types of safeguards and how these devices protect your workers. We also reveal the four types of machine safeguards, and three types of hazardous mechanical motion, that are vital to any workplace.
What is the Key Element of Any Safeguarding System?
The key element of a reliable safeguarding system is to provide specific, detailed training to your employees. Educating your operators is decided internally, but you must have a solid plan in place to ensure that training is effective.
How do you plan a successful machine guarding project? There are 3 vital components to ensure a reliable system, including:
Identifying vulnerable areas.
Preventing access to hazardous parts.
Improving awareness for operators and leadership.
Empowering operators to halt operations in emergency situations.
Collaborating with third-party professionals to minimize subjectivity.
What Do Safeguarding Devices Do to Protect Your Workers?
Safeguarding devices are designed to protect workers from hazardous mechanical motions and unexpected contact with machine parts. The most common physical safeguard is a guard, which completely encloses the potential hazard or restricts access through interlocking mechanisms.
Guards can be any type of barrier, gate, fence, or other enclosure that makes it difficult for anyone to reach or come in contact with the hazardous area. Other common safeguards include perimeter guarding that restricts access to unauthorized persons.
Safety devices like these empower your workers to operate with confidence. When your workers feel that their safety is prioritized, they can focus on optimizing productivity and increasing output.
What are the 4 Types of Machine Safeguarding per OSHA?
According to the Occupational Safety and Health Administration (OSHA), there are four types of guards used in machine safeguarding systems. These include:
Fixed Guards
Interlocked Guards
Adjustable Guards
Self-Adjusting Guards
Fixed Guards
Fixed guards are stationary devices that are used to protect workers from exposure to hazardous moving parts. They remain in a fixed position and do not move when the machine is in use. Examples of these include barrier guards, light curtains, and two-hand control devices.
Interlocked Guards
Interlocked guards provide an extra layer of protection. These devices stop the machine if a guard or shield is removed or opened while the machine is in operation.
These guards are designed with electrical switches which detect if any shield or guard has been moved out of its original position. This enables them to shut off the machinery immediately before anyone can be injured by it.
Adjustable Guards
Adjustable guards are used when access to the hazardous area needs to be periodically changed for cleaning or maintenance purposes. These guards are designed to be manually adjusted and provide variable protection that can be adapted to different working conditions.
Self-Adjusting Guards
Self-adjusting guards are used when the machine is under constant use with frequent operator access needed. These guards are designed in such a way that they automatically adjust themselves according to the movements of the worker, so there is no need for manual adjustment or interruption of operation.
Familiarize yourself with these 4 types of safeguarding solutions to optimize the safety and productivity of your operations. The next step is understanding what hazardous motions exist within machines, which we discuss below.
3 Types of Hazardous Mechanical Motion
According to OSHA, the 3 types of hazardous mechanical motion include:
Rotating Machine Parts
Reciprocating Motions
Transverse Motions
Rotating Machine Parts
Rotating machine parts can be dangerous due to the possibility of being exposed to pinch points and flying objects. This type of motion includes saws, drills, lathes, and other machines with spinning parts that could cause harm if not properly guarded.
Reciprocating Motions
Reciprocating motions involve back-and-forth or up-and-down movements. If unguarded, this type of motion is hazardous because workers can get their hands, fingers, and body parts entrapped in any openings. Common types of machinery that employ this kind of motion are presses and punching machines.
Transverse Motions
Transverse motion involves a linear movement across an axis, such as with conveyor belts and transfer machines. Safety guards must be carefully placed to protect employees from coming into contact with the moving parts.
5 Proven Ways Safeguarding Solutions Enhance Productivity
It’s important to note that while machine safeguarding protects workers, it also has the potential to improve productivity. In fact, there are several proven ways that machine safeguarding solutions can enhance workplace operations:
Increased Visibility
Maximized Confidence
Improved Efficiency
Reducing Maintenance Costs
Optimized SOPs
1. Increased Visibility: Safeguarding devices provide clear lines of sight for both workers and supervisors, allowing for better communication and better machine operation.
2. Maximized Confidence: Operating without fear of injury empowers your operators to focus more time and energy on the task before them.
3. Improved Efficiency: Safeguarding devices minimize downtime and streamline your processes. With maximum confidence, your workers can move at their optimal pace.
4. Reduced Maintenance Costs: When machines are regularly inspected and maintained using proper safety procedures, you save money on repairs by catching minor issues before they become major problems.
5. Optimized SOPs: As your operators and leadership become increasingly proficient, it becomes easier to standardize procedures and train new employees.
How Does Machine Safeguarding Enhance Productivity?
Our safety experts will dissect each of these benefits in greater detail next month. Additionally, we’ll reveal:
Why you need an expert to implement safeguarding solutions successfully.
How to find experienced machine safety solution providers.
Insider secrets about the value of a proactive, professional approach.
Even small, do-it-yourself projects often require consultation with safety specialists. Stay tuned to our safety blog to learn more!
Learn How to Safeguard Your Machines with Stronghold Safety Engineering
With the right machine safeguarding solutions in place, you can improve safety for your employees, and productivity in your operations. To learn more about the value of safety, safeguarding, and compliance, reach out to our team today.