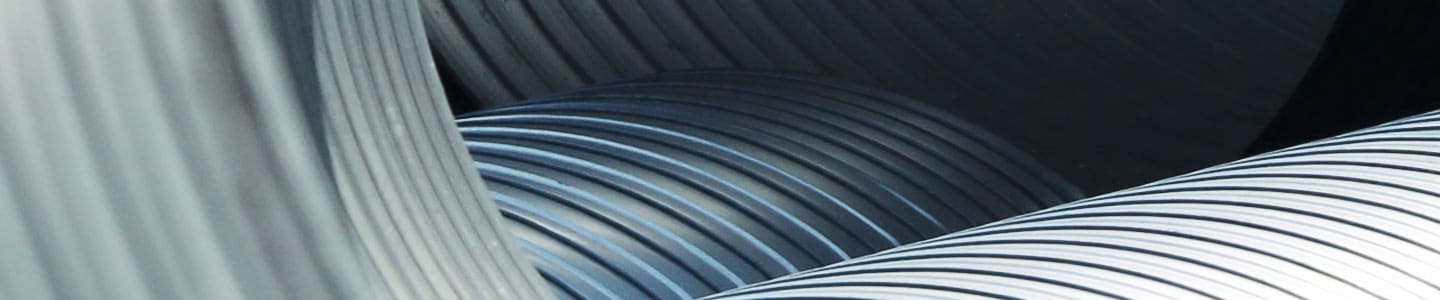
OSHA Inspection Checklist: Is Your Business Prepared?
June 19, 2024
OSHA Inspection Checklist: Is Your Business Prepared?
An OSHA inspection can be a stressful experience for any business owner. But these inspections don’t have to be challenging if you maintain a safe workplace environment. One of the best ways to prepare for an OSHA inspection is to use an internal OSHA inspection checklist.
In this article, we'll discuss the importance of having a working OSHA inspection checklist, as well as provide suggestions for creating your own checklist. For more information, you can visit the OSHA website.
Why is an OSHA Inspection Checklist Important?
Preparing an OSHA inspection checklist can provide many benefits for businesses. Most important, it can help ensure OSHA compliance, reducing the risk of costly fines and penalties. Following the guidelines outlined in the checklist helps ensure businesses are maintaining a safe workplace.
In addition, an OSHA inspection checklist can help businesses identify hazards and areas for improvement in their safety programs. By conducting a mock inspection and reviewing the checklist, businesses can proactively identify areas where they may be falling short and take steps to address these issues before an OSHA inspector arrives.
Finally, an OSHA inspection checklist can help reduce stress and anxiety around OSHA inspections. By having a clear plan in place and knowing what to expect, businesses can approach the inspection with greater confidence and ease.
What to Include on an OSHA Inspection Checklist
Using an OSHA inspection checklist effectively requires careful planning and preparation. Here are some items you should include on your self-inspection checklist if they are applicable to your business operations.
General Safety Practices
Are all employees trained in basic safety practices, such as proper lifting techniques and emergency procedures?
Are safety procedures communicated effectively and regularly reviewed?
Is the workplace clean and free from clutter?
Are walkways and work areas free from obstructions and properly marked?
Is an active safety program for employee health and safety maintained by a clear administrator?
Is the minimum amount of restrooms provided for employees?=
Workplace Environmental Controls
Do all the work areas have the proper lighting?
Do all the work areas have the proper ventilation systems?
Is water for drinking, cooking, and washing potable?
First Aid
Are stocked first aid kits available in all work areas?
Are eyewash stations, or sinks or showers, available for flushing eyes?
Do employees receive adequate first aid training and instruction for emergency situations?
Hazard Communication
Are all hazardous materials properly labeled and stored?
Are employees trained in the safe use and handling of hazardous materials?
Is there a written hazard communication program in place?
Electrical Safety
Are electrical panels properly labeled and accessible?
Are electrical cords and outlets in good condition and not damaged?
Are employees trained on the safe use of electrical equipment?
Machine Safety
Are machines properly guarded to prevent employee injury?
Are employees trained in the safe use of machines and equipment?
Are lockout/tagout procedures in place and being followed?
Fire Safety
Are fire exits clearly marked and unobstructed?
Is the fire alarm system certified and tested annually?
Are fire extinguishers easily accessible and in good working order?
Are employees trained on the proper use of fire extinguishers and other fire safety procedures?
Personal Protective Equipment (PPE)
Are employees using appropriate PPE for the tasks they are performing?
Are PPE training and maintenance programs in place?
Walkways
Are non-slip materials used on wet surfaces for better traction?
Are holes in walking surfaces covered or repaired?
Are handrails or guardrails provided where necessary?
Are all equipment and machinery located in a safe and secure location, away from walkways?
Ladders
Do all employees have training for safe ladder usage?
Are all ladders maintained and in good working order?
Are ladders placed on stable, level surfaces?
Are the steps or rungs free of grease, oil, or other slippery substances?
Exits
Are all exits free from obstructions?
Are all exits unlocked during working hours?
Are all exit signs labeled, illuminated, and clearly visible?
Are exit routes clearly marked and free of obstructions?
Fall Protection
Are employees provided with fall protection equipment when working on ladders at heights greater than 6 feet?
Is fall protection equipment in good condition?
Are employees trained on the proper use of fall protection equipment?
Are guardrails, safety nets, personal fall arrest systems (PFAS), or other appropriate fall protection measures in place for employees performing rooftop work?
Emergency Preparedness
Is there a written emergency action plan in place?
Are employees trained on emergency procedures?
Are emergency exits and evacuation routes clearly marked and unobstructed?
Hand & Power Tools
Are all tools properly maintained and in good working condition?
Are tools stored in designated areas when not in use?
Are all employees trained in the safe use of tools they use?
Are tools equipped with safety guards or other safety devices?
Machine Guarding
Are all machines equipped with appropriate guards to prevent employee contact with moving parts, points of operation, and other hazards?
Are all machines equipped with emergency stop buttons or other emergency shut-off devices that are clearly labeled and easily accessible?
Are all guards appropriate for the type of machine and the nature of the hazards they are designed to protect against?
Are power shut-off mechanisms within reach of operators?
Forklifts
Are all operators trained and authorized to operate a forklift?
Are all brakes, steering, controls, and safety devices in good working condition?
Are all forklifts properly labeled with capacity ratings, operating instructions, and warning labels?
Welding and Cutting
Are all welders and cutters properly trained and authorized to perform their tasks?
Are all welding and cutting equipment properly maintained and inspected before each use to ensure they are in good working condition?
Are all nearby areas protected by fire-resistant shields or barriers?
Are all workers properly trained in safe work practices for welding and cutting?
Are all workers following safe work practices, such as properly storing and handling compressed gas cylinders?
Compressed Air Receivers
Are all compressed air receivers equipped with pressure relief valves and pressure gauges?
Are all compressed air receivers properly maintained and inspected in accordance with the manufacturer’s recommendations?
Are all workers properly trained in safe work practices for working with compressed air systems?
Recordkeeping
Are OSHA 300 logs and other required records properly maintained?
Are employees trained in the proper completion of injury and illness reports?
Your Machine Safety OSHA Compliance Specialists
It is important to note that the specific checklist requirements will vary depending on the type of business, industry, and location. At Stronghold Safety, we have a successful track record assisting businesses identify machine safety risks and hazards to help ensure the safety and health of their employees.
As expert machine safety OSHA compliance consultants, we can help you create an effective machine safety risk assessment checklist that fits your business's needs. Please contact us today to maintain OSHA standards with your machine operations.