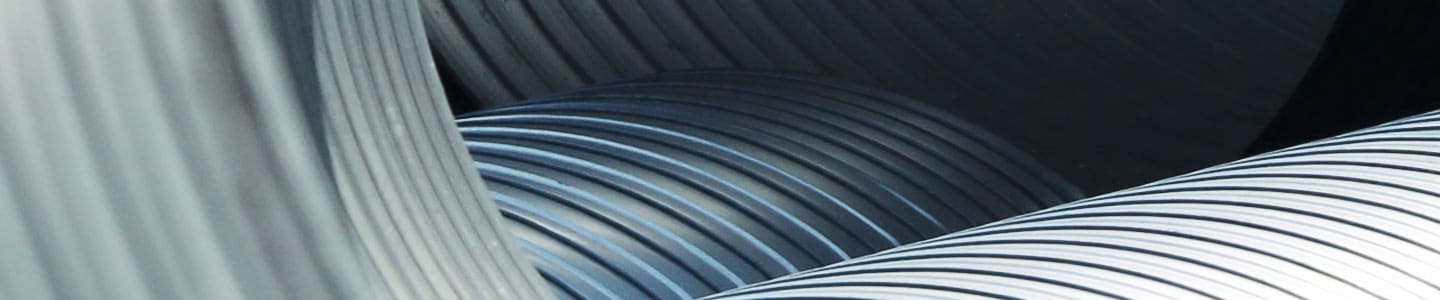
6 Ways to Reduce Risk in the Warehouse
June 19, 2024
6 Ways to Reduce Risk in the Warehouse
Safety risks identify hazards that are present in every warehouse, many of which often go unnoticed until it’s too late. By addressing and monitoring them, you facilitate a safe environment that protects employees and maximizes ROI.
Additionally, they can also reduce employee morale, and sometimes they even lead to major fines and lawsuits. That’s why it’s critical that you never underestimate the importance of warehouse safety management.
At Stronghold® Safety, we have over 15 years of experience in industrial and warehouse risk assessments and workplace safeguarding. To share what we’ve seen in that time, we present the 6 best practices for reducing risk in your warehouse, below.
What are the Most Common Warehouse Risks?
There are several common risks associated with warehousing establishments, such as strain, fall hazards, and exposure to heavy machinery.
However, according to the most recent data that we could access from the Occupational Safety and Health Administration (OSHA), the 10 fire risks that they tend to cite most frequently are related to:
Forklifts
Hazard communication
Electrical wiring methods
Electrical system design
Guarding openings/holes in floors & walls
Exits
Mechanical power transmission
Respiratory protection
Lockout/Tagout
Portable fire extinguishers
How Can You Reduce Risk in Your Warehouse?
If you take a closer look at that list, you’ll realize that each entry can be addressed with one of these six, simple warehouse safety tips:
Preparation & Strategy
Machine Safeguarding
Electrical Safeguarding
Fall Protection
Education
Signage
1. Preparation
The proverbial “Square One” for any serious project, proper preparation ensures that you have a clear, low-level view of the risks your operators take every day. This empowers you to be as comprehensive as possible when outlining your plans of action.
At Stronghold®, we recommend a professional risk assessment and reduction consultation from industry experts. Unless you’re a Subject Matter Expert in each process you oversee, it’s beneficial to seek out an objective perspective.
2. Machine Safeguarding
Professional safeguarding is a no-brainer for every industrial workspace. Many serious injuries prevent accidents that occur every day could be prevented simply by implementing the right blade guard, safety shield, or other protective element.
Industrial machinery is dangerous and needs to be treated as such. Take steps today to implement safeguarding on the heavy equipment in your warehouse.
3. Electrical Safeguarding
High-voltage components in warehouses’ electrical systems can pose a serious threat to employees.
Emergency stops, motor controls, and light curtains are all other control elements that can be safely implemented to reduce risk and the likelihood of injury.
Make sure your employees have the electrical safeguarding equipment they need to remain productive without concern of potentially life-threatening injury.
4. Fall Protection
Injury due to falling is the top OSHA citation, overall. Therefore, your warehouse needs to take preventative measures to reduce the risk of falls in all potentially hazardous areas.
Safety gates and perimeter guarding are both easy ways to protect against this all-too-common threat. Not only can falls cause injuries to your employees, but they also slow production throughout the warehouse.
Take steps today to prevent falls and reduce the figure of an alarming OSHA statistic.
5. Education
A lack of adequate training and information is the most common cause of injury in the workplace. In fact, several of OSHA’s most common warehouse citations hint at a lack of sufficient education.
It’s up to you to ensure your employees are aware of all of the hazards in their environment. Moreover, you must make certain that they’re always up to speed on the precautions necessary to maintain proper safety.
Education is an ongoing process and one that needs to be kept up with as changes and upgrades are made to your warehouse. As a workspace evolves, so do the needs of its safety plan.
6. Safety Signage
Any hazardous zones in your warehouse need to be clearly identified, labeled and marked off with safety signs (such as paint, tape, and placards) to make them clearly recognizable to all employees. This starts with identification.
A professional safety assessment of your warehouse will point out any dangerous areas and suggest changes that can increase protection for your employees. This will also heighten your operators’ awareness of identifying hazards and make them more likely to notice any threats in the workplace.
Comprehensive Safety Training: The Foundation of Warehouse Safety
The cornerstone of minimizing risk in any warehouse setting begins with comprehensive safety training. This involves regular, detailed sessions that cover all aspects of warehouse operations, from handling equipment to navigating common hazards. Training should be dynamic, incorporating both theoretical knowledge and practical, hands-on experience. By ensuring every team member is well-versed in safety protocols, we create a culture of awareness and responsibility.
Advanced Equipment Handling Techniques
It’s crucial to equip our workforce with advanced techniques for handling warehouse equipment and hazardous substances. This includes training on the latest machinery, understanding the nuances of material handling, and staying updated with industry best practices. Specialized training sessions focused on equipment handling can significantly reduce the likelihood of accidents, ensuring a safer work environment.
Optimizing Warehouse Layout for Safety
An optimized warehouse layout is key to minimizing risks. This involves strategic placement of goods, clear signage for hazardous areas, and ensuring unobstructed pathways. Regular audits of the warehouse layout to both identify potential hazards and risk zones and making necessary adjustments can lead to a significant reduction in accidents and injuries.
Implementing Cutting-edge Technology for Risk Management
Leveraging technology can play a pivotal role in risk reduction. From automated surveillance systems that monitor safety compliance to wearable tech that tracks workers’ health metrics, technology offers innovative solutions to traditional safety challenges. By integrating these technologies, we can anticipate potential risks and take proactive control measures, to mitigate them.
Regular Health and Safety Audits
Conducting regular health and other inspections and safety audits is crucial for maintaining a safe warehouse environment. These audits help in identifying potential hazards, assessing the effectiveness of current safety measures, and determining areas for improvement. An audit should be thorough, covering every aspect of the warehouse operations, and should lead to actionable insights that enhance overall safety.
Enhanced Emergency Response Protocols
A key aspect of risk assessment and management in a warehouse is the development and implementation of enhanced emergency response protocols. These protocols should be clear, concise, and easily accessible to all employees. Regular drills and training sessions on emergency response can drastically improve the readiness and effectiveness of the team in handling unforeseen situations, thereby reducing potential hazards.
Stressing the Importance of Personal Protective Equipment (PPE)
The use of Personal Protective Equipment (PPE) is essential in maintaining a safe warehouse environment. Ensuring that all employees and warehouse managers are equipped with the necessary PPE, such as helmets, gloves, safety glasses, and appropriate footwear, and are trained in their correct usage, plays a crucial role in injury prevention. Regular checks and maintenance of PPE also ensure that they provide optimal protection at all times.
Fostering a Culture of Safety Awareness
Creating a culture where every employee is an advocate for safety is vital. This involves encouraging open communication about safety concerns, recognizing and rewarding safe practices, and ensuring that safety is a shared responsibility. A culture of safety awareness not only helps in reducing risks but also enhances overall employee morale and productivity.
Leveraging Data Analytics for Predictive Safety Measures
Data analytics can be a powerful tool in predicting and preventing warehouse risks. By analyzing accident reports, equipment usage data, and employee feedback, we can identify patterns and predict potential risk areas. This proactive approach allows for risk assessments and the implementation of preventive measures before accidents occur, further enhancing warehouse safety.
Reduce Risk in Your Warehouse with Stronghold® Safety
If you haven’t been taking warehouse risk management seriously, then it’s time to start. These six top warehouse risk assessments and safety steps are some of the ways you can improve the lives of your employees and the production of your business.
At Stronghold® Safety, we specialize in delivering comprehensive safety plans for industrial workspaces. We also carry a complete line of industry-leading safeguarding, electrical, and fall protection products.To research, develop, and implement a safety plan for your warehouse, reach out to our team today.